Winter Homebuilding in Wisconsin: Challenges & Solutions
Written By Dustin Harpe
Building a home in Wisconsin during the winter months presents unique challenges, but with the right strategies, it can be a successful and efficient process. While frigid temperatures, snow, and shorter daylight hours pose obstacles, modern construction techniques and proper planning can mitigate these issues. Here, we explore the challenges of winter homebuilding in Wisconsin and practical solutions Harpe Development uses to overcome them.
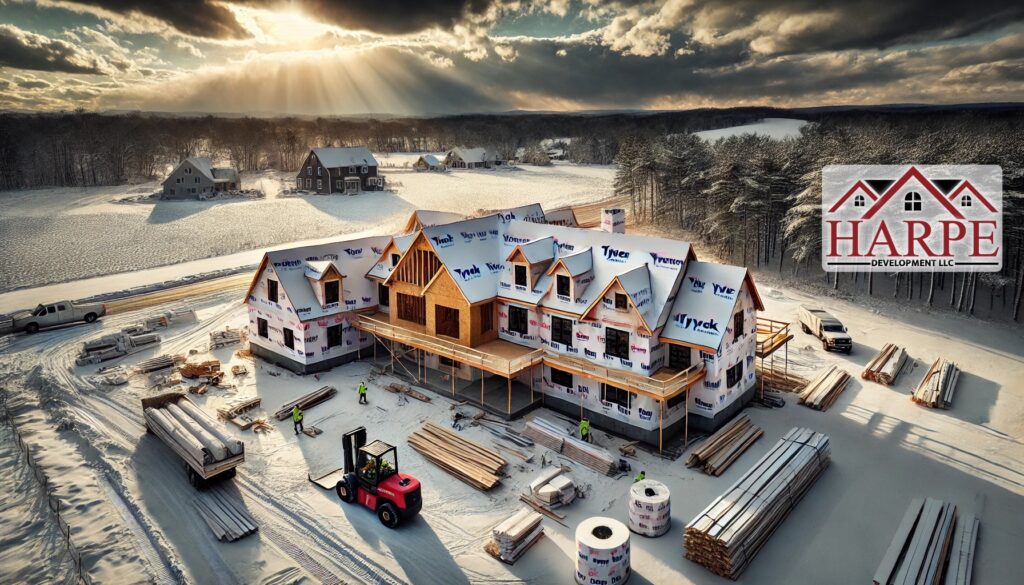
Challenges of Winter Homebuilding
1. Freezing Temperatures
One of the biggest hurdles of winter construction is the freezing temperatures, which can impact everything from foundation pouring to material handling.
- Concrete Setting: Concrete requires specific conditions to cure properly. Cold weather can slow or prevent proper curing, leading to weakened foundations.
- Worker Safety: Construction workers are at higher risk of frostbite and hypothermia when working in extreme cold.
- Equipment Functionality: Machinery and tools may operate less efficiently or even fail in subzero temperatures.
2. Snow and Ice Accumulation
Wisconsin winters bring heavy snowfall and ice, which can create hazardous conditions at construction sites.
- Site Accessibility: Snow can block roads and make transportation of materials difficult.
- Structural Load Concerns: Snow accumulation on partially built structures can add significant weight and stress.
- Worker Safety Risks: Ice increases the likelihood of slips and falls, making job sites more dangerous.
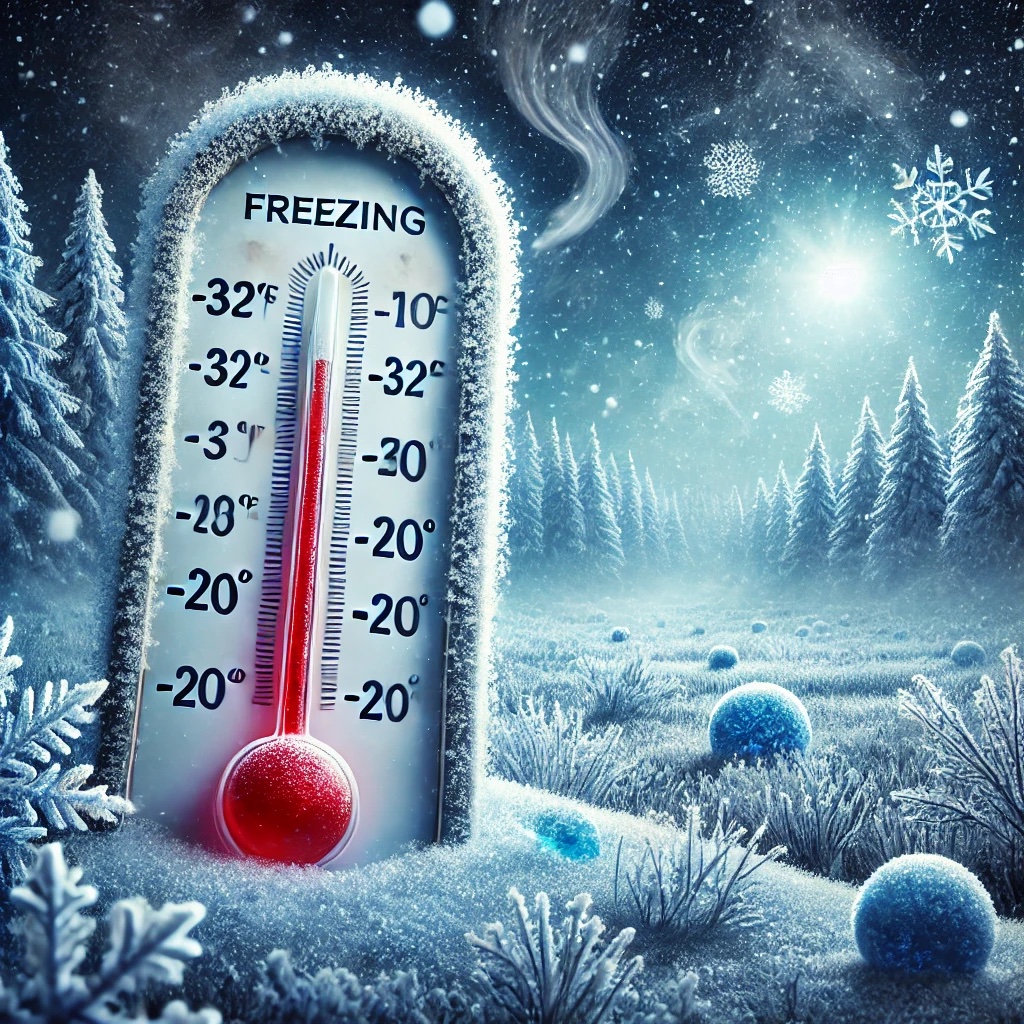
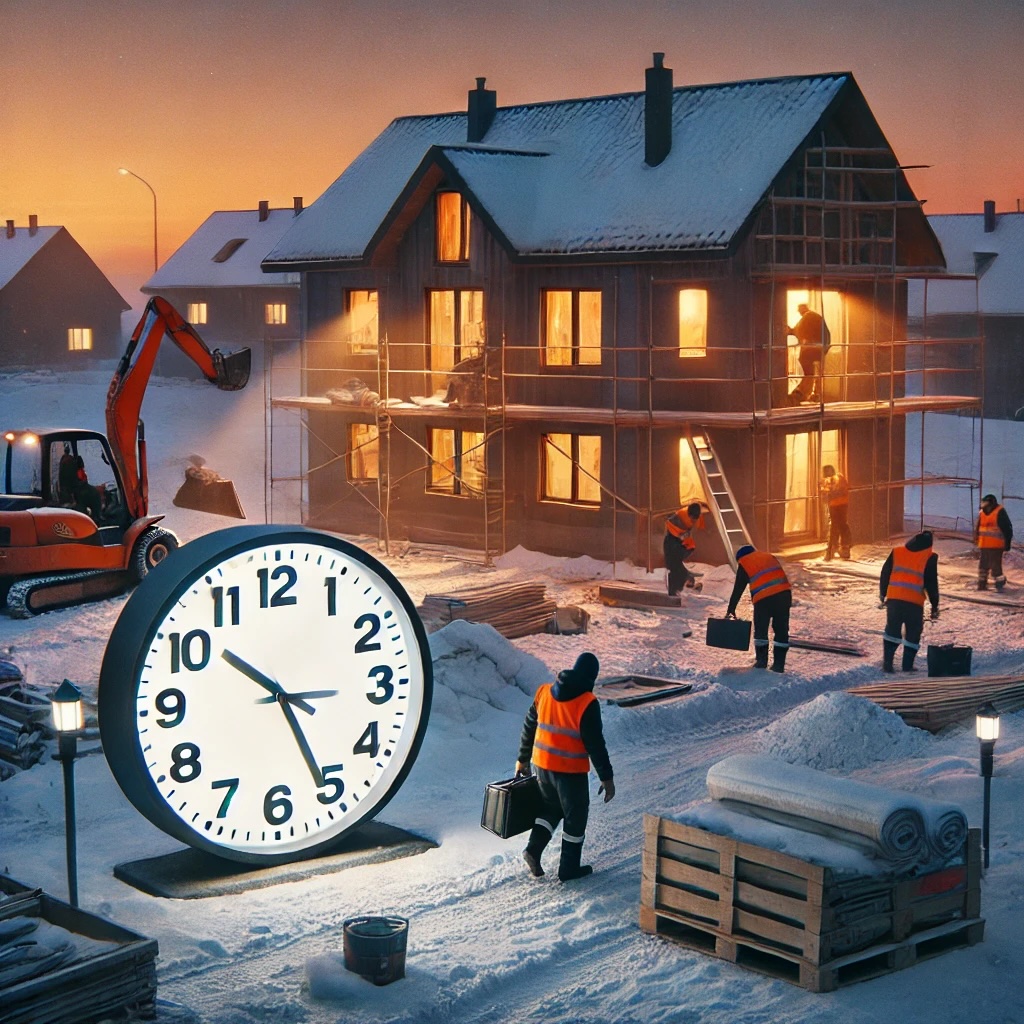
3. Shorter Daylight Hours
With fewer daylight hours in the winter, crews have less time to complete daily tasks, potentially extending project timelines.
- Visibility Issues: Less natural light can reduce visibility, increasing the risk of accidents and errors.
- Extended Timelines: Shorter workdays may lead to project delays, increasing overall labor costs.
4. Material Handling and Storage
Certain building materials are sensitive to cold temperatures, requiring special handling and storage.
- Lumber and Drywall: Moisture from snow and ice can cause warping, swelling, or mold issues. Material outside can also disappear underneath the snow that you don’t find until spring time.
- Sealants and Adhesives: Some products may not adhere properly in low temperatures.
- Paint and Finishes: Many paints and coatings require temperatures above freezing to dry and cure properly.
Solutions for Winter Homebuilding
1. Proper Planning and Scheduling
Strategic planning is essential to successfully navigate winter construction.
- Pre-order Materials: Ensure materials are delivered and stored in weather-protected areas before winter sets in.
- Schedule Accordingly: Plan tasks that are less affected by cold (e.g., interior work, electrical, and plumbing) during the coldest months.
- Use Weather Forecasting Tools: Regularly monitor weather conditions and adjust schedules as needed to optimize working conditions.
2. Cold-Weather Construction Techniques
Builders can use specialized techniques to work efficiently despite the cold.
- Heated Enclosures and Temporary Shelters: Erecting temporary heated enclosures allows necessary scopes like exterior masonry to cure properly.
- Ground Thawing Methods: Using ground heaters and insulating blankets can prevent frost from affecting excavation and footings for foundation work.
- Anti-freeze Additives: Special additives can be mixed into concrete to accelerate curing and prevent freezing damage.
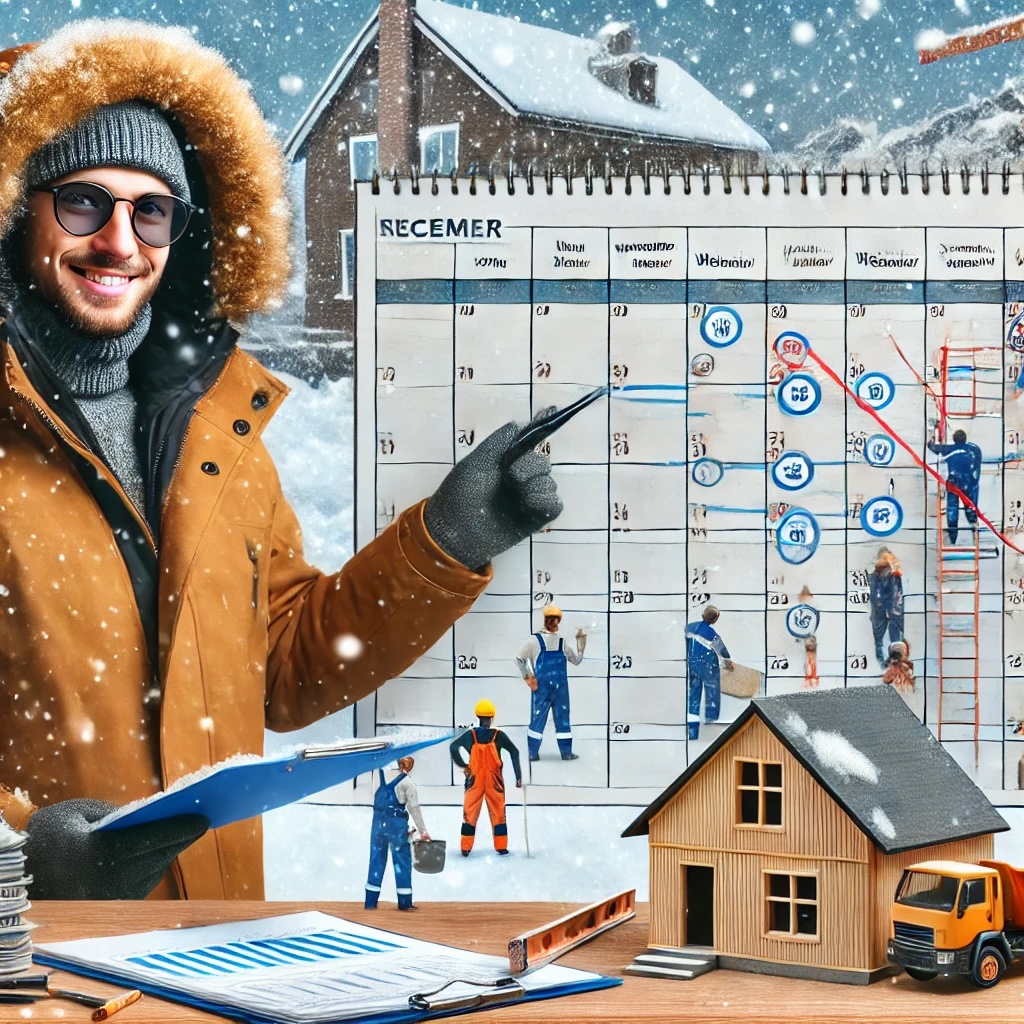
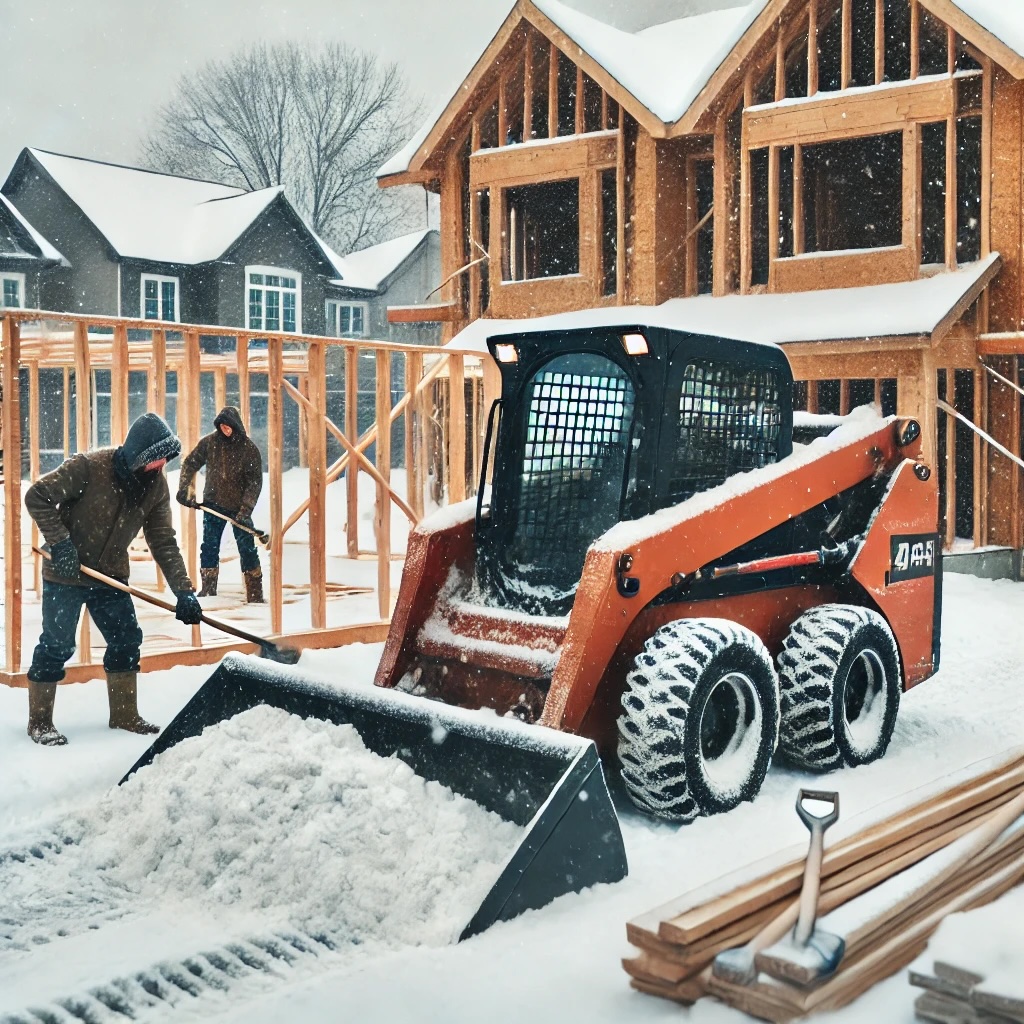
3. Snow and Ice Management
Keeping the job site clear of snow and ice is critical for safety and efficiency.
- Regular Snow Removal: Assign a dedicated team to clear pathways, roofs, and work areas.
- De-icing Solutions: Use salt or sand on walkways to prevent slipping hazards.
- Covering Materials: Store materials in heated or covered spaces to protect them from snow and ice damage.
4. Artificial Lighting and Extended Work Hours
Addressing the challenge of limited daylight can help keep projects on track.
- Portable Lighting Systems: Use high-powered LED lights to maintain visibility on-site.
- Adjust Work Shifts: Starting work earlier in the day and using artificial lighting in the evening can maximize productivity.
5. Worker Protection and Safety Measures
Ensuring worker safety and comfort is crucial during winter construction.
- Cold-Weather Gear: Provide insulated gloves, jackets, and boots to keep workers warm.
- Heated Break Areas: Set up heated tents or trailers where workers can take breaks and warm up.
- Regular Safety Training: Educate workers on recognizing symptoms of frostbite and hypothermia to prevent health risks.
Conclusion
Winter homebuilding in Wisconsin comes with its share of challenges, but with proper preparation and the right techniques, it can be accomplished efficiently. By leveraging cold-weather construction methods, maintaining worker safety, and effectively managing snow and ice, builders can keep projects on schedule while ensuring high-quality results. Whether building a custom home or a large-scale development, tackling winter construction head-on with strategic planning and modern technology will lead to success even in the harshest Wisconsin winters.